Computer Numerical Control (CNC) lathe is a modern computer-controlled lathe normally used for machining a workpiece that is clamped and rotated around a stationary carving, cutting, or shaping tool, which is also part of the machine.
Table of Contents
What is a lathe?
To begin with, a lathe is a machining tool used to construct a workpiece. The workpiece is clamped and rotated to be carved, cut, or shaped using a stationarily mounted tool. Heads and bits are also used to remove unwanted parts, leaving a nicely shaped workpiece.
A workpiece is any object, usually wood or metal, that is processed into the desired shape using a tool or a machine. Machining is the process of removing material, typically metal, to create parts for machines, tools, transportation, and more. Almost all sectors utilize lathe for a variety of purposes so, ametals.com called it the “mother of machining tools.”
Let us take the potter’s wheel as an example. The wheel is the lathe keeping the workpiece – the clay – in one place and is rotated at the desired speed. The carving, cutting, or shaping tool is the potter’s hand, moving along the length (“y” axis) and in and out toward the center (“x” axis) of the clay.
Also read How To Know If Your Computer Has A Virus.
What is a Computer Numerical Control (CNC)?

Computer numerical control (CNC), according to Essex (2021), is a method of automating the control of machine tools through the use of software embedded in a microcomputer attached to the tool. CNC is commonly used in manufacturing for machining metal and plastic parts.
Engineers identify parts to be manufactured, create a computer-aided design (CAD) drawing, and translate the drawing into a custom computer program called G-code. This G-code is stored in and executed by a microcomputer attached to the machine called the machine control unit (MCU). This program instructs the machine of the materials’ feed rate, the positioning and speed rate of tools, and other set parameters.
Some CNC technology systems are integrated with computer-aided manufacturing (CAM) software which can speed the process of programming the MCU. Machine control is programmable and repeatable. CNC provides more precision, accuracy, speed, flexibility, consistency, and complexity. This provision incurs fewer errors, cheaper operations, and less waste of material throughout the manufacturing process.
CNC can also automate the operation of mills, routers, grinders, and lasers, other than lathes. It can control non-machine tools, such as welding, electronic assembly, and filament-winding machines.
CNC requires companies to hire a skilled CNC programmer and/or an operator to perform test runs and ensure machine performance and maintenance.
What is Computer Numerical Control (CNC) lathe?

CNC lathe is a machine tool operated by MCU, which is integrated with CAD or CAM. It clamps and rotates the workpiece around a stationary carving, cutting, or shaping tool that moves in various axes. To simply put, it is a lathe automated by a CNC system.
CNC lathes with 2 axes are called CNC turning machines because of the rotating action of the part. They are called turning centres when they have additional axes, sub-spindles, or any other specified parts. The choice for more additional parts depends on the complexity of manufacturing needs.
CNC lathes are ideal for prototyping and limited runs. Though pricey, they provide quicker manufacturing turnaround and entail cheaper costs for hiring and monitoring staff. Only one or a few people can monitor multiple CNC lathes at the same time. They are fully automated so their heads can hold different bits to execute different processes: grinding, refining, sanding, and polishing. They can also mill (rotate a cutting tool against a still workpiece), drill (make holes), bore (enlarge a hole made by another process), and tap (produce internal threads). After programming multiple steps, a single machine can take a single workpiece from raw material to finished product.
Main Parts of a CNC lathe

Below is a list of a CNC lathe’s main parts and their brief descriptions. Depending on the complexity of manufacturing needs, CNC lathes may have additional parts.
- Headstock
It contains the machine’s main motor. It drives the main spindle where the chuck is mounted.
- Bed
Hardened by design to withstand any kind of machining, it is where the tool turret travels.
- Chuck
It vises workpieces for machining. Its many parts are mounted with various jaws, which are appropriate for the workpiece to be machined.
- Tailstock
This is located at the other end, opposite the chuck. It provides the chuck extra force for clutching the workpiece.
- Main Spindle
It is the rotating part of the lathe, equipped with centers, chucks, and faceplates that hold the workpiece.
- CNC Control Panel
Since this is where the MCU is located, it is considered the brain of the machine. It controls the whole CNC lathe. Operators use the keys in the panel to start or stop the machine, move the axis, or input new programs through its ports.
- Tool Turret
This is where tools are mounted for workpiece machining. It varies in shape and in the number of tools to be mounted on it for specific machining needs.
Uses of a lathe

Manufacturing, automotive, aerospace, electronics, medical, sports, and music sectors, to name a few, can prove the usefulness of CNC lathes. Machinefanatic listed thermal spraying, metalworking, woodturning, metal spinning, reclamation of parts, pottery shaping, and glasswork as examples of processes they are used for.
Firearms; bowls; musical instrument bodies; sporting goods such as baseball bats and cue sticks; driveshafts of cars; and table legs are a few examples of finished products the CNC lathes can manufacture.
About Author
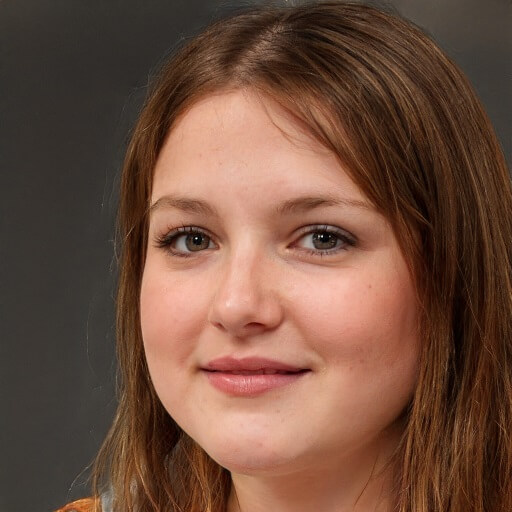
Bailey Hudson is a Freelance Business Writer. She had worked with companies all over the world on both inbound and outbound marketing writing. Here are Bailey’s other articles you can follow. https://baileyhudson.contently.com/